A Day to Remember
This is the anniversary of the 9/11 terrorist attacks on America, and on the world.
Once again, it is a day to reflect and remember. In fact, we who experienced the events of that day in any way must remember and share, lest we not forget. If you don’t know about what happened that day, then you must become educated, and made aware of the events of that day in New York, Washington and Somerset County, Pennsylvania. It was an attack driven by hate, and an attack on all of us.
There is a saying that you die three times: when you take your last breath; when they cover your grave after your funeral; and when your name is uttered for the last time.
This is what I remember, and what I choose to reflect upon every year on this day. You will indulge me, I hope, because it is necessary for me to share this with others and share it every year on this day for as long as I can do so. It is the least I can do for a shipmate.
So, join me in saying his name: Michael Noeth.
*** Linseed oil:
Some things have an evocative smell.
When I was in command of the Naval Media Center in Washington, D.C., the executive officer of a ship based at Pearl Harbor – USS Russell (DDG 59) – called my staff at All Hands magazine in our Publishing Department. The XO had a Sailor aboard the ship who wanted to be a draftsman.
The “undesignated seamen” or SNs on a ship usually work in the deck force, chipping paint and handling lines. As they see what professional opportunities are available on board their ship, they can “strike” for a rating, like Radioman or Quartermaster. A “Striker Board” will convene and review the needs of the ship, and the desires of the individual. If the Sailor is squared away, has done a good job with the deck force and the ship needs a Quartermaster (QM), for example, he or she can strike for that rating, and becomes a QMSN.
Seaman Michael Noeth wanted to be a Draftsman. The DM rating was one of the smallest ratings in the Navy. There were very few of them compared to Gunner’s Mates or Machinist’s Mates, and certainly none aboard a surface combatant. In fact, today the rating has been disestablished and the functions combined into the Mass Communications Specialist (MC) rating.
In this case, the executive officer wanted to do something good for his Sailor. And this was extraordinary, because USS Russell was about to depart on deployment. In spite of the fact that the ship was about to be on cruise for six months, the XO called us and asked if his Sailor could come and work with us to learn the DM rating so he would be prepared to take the DM test for Third Class Petty Officer. If he passed, he could become a DM3. If not, he could return to the ship and eventually strike for another rating. For our part of the deal, we had to cover his travel expenses. We said yes.
There are never enough Sailors in the Deck Force, especially on deployment, but the XO wanted to help a Sailor. So, SN Michael Noeth came to work for us in the Publishing Department at the Naval Media Center in Washington, D.C.
He was placed under the expert tutelage of our Draftsman First Class (DM1) Rhea Mackenzie. Seaman Noeth quickly made himself at home in a back corner of the All Hands magazine production spaces. And it was here he set up his easels, canvasses a and paints. When I would come by — which was often, because I was always wandering around Building 168 to see all of the interesting stories and projects our people were working on — I could smell the linseed oil he used for his brushes long before I reached his work area. He would have various canvasses and illustrations in various stages of completion posted around his desk, as well as examples of artwork he admired or wanted to emulate.
As one of the 450 men and women of the Naval Media Center, he learned his trade from an experienced draftsman, created artistic content for All Hands magazine, and became a well-liked and contributing member of the command. At our Halloween party, he came in second place in our costume contest. He was a dead ringer “Alex” from Clockwork Orange, and was topped only by an even more convincing Cruella Deville from 101 Dalmatians.
Whenever I got near his work area, I would be greeted by the smell of his linseed oil, and I knew I would be in for some kind of surprise. Seaman Noeth painted the cover for several issues of All Hands magazine (such as the one with a cut-out porthole that opened to an ocean panorama. To see him tackle these assignments was a joy, probably because he was enjoying his work, and appreciative of the opportunity. On my visits, I would see the many versions and sketches he was working on, and I could see it all come together with the finished product.
He took the advancement exam and passed it. As his six-month temporary assignment came to an end, his command allowed him to transfer to my command on a permanent basis as they did not have any billets for a draftsman, and we did. Soon, he moved on to other Navy assignments as a Draftsman, all because his ship wanted to give him a chance to realize his dream, and my command wanted to help him get there. We felt good about helping him attain his goal. But most of all, because he was a Sailor who deserved it.
He did, indeed, become a talented Navy illustrator and draftsman. He served aboard amphibious assault ship USS Wasp (LHD 1), and was later assigned to the Navy Command Center where he skillfully created briefings and presentations for Navy leadership. He was doing just that on September 11, 2001, when terrorists forced an airliner to crash into that building.
We must not forget. So, I choose to remember a bright, ambitious, creative young striker today, and whenever I smell linseed oil.
We will continue to speak his name.
-30-
Please also see:
https://allhands.navy.mil/Stories/Display-Story/Article/1839561/we-will-never-forget/
https://www.washingtonpost.com/wp-srv/metro/specials/attacked/victims/v_358.html
https://pentagonmemorial.org/explore/biographies/dm2-michael-noeth-usn
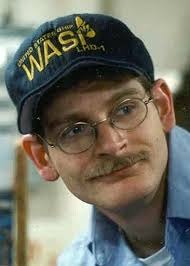