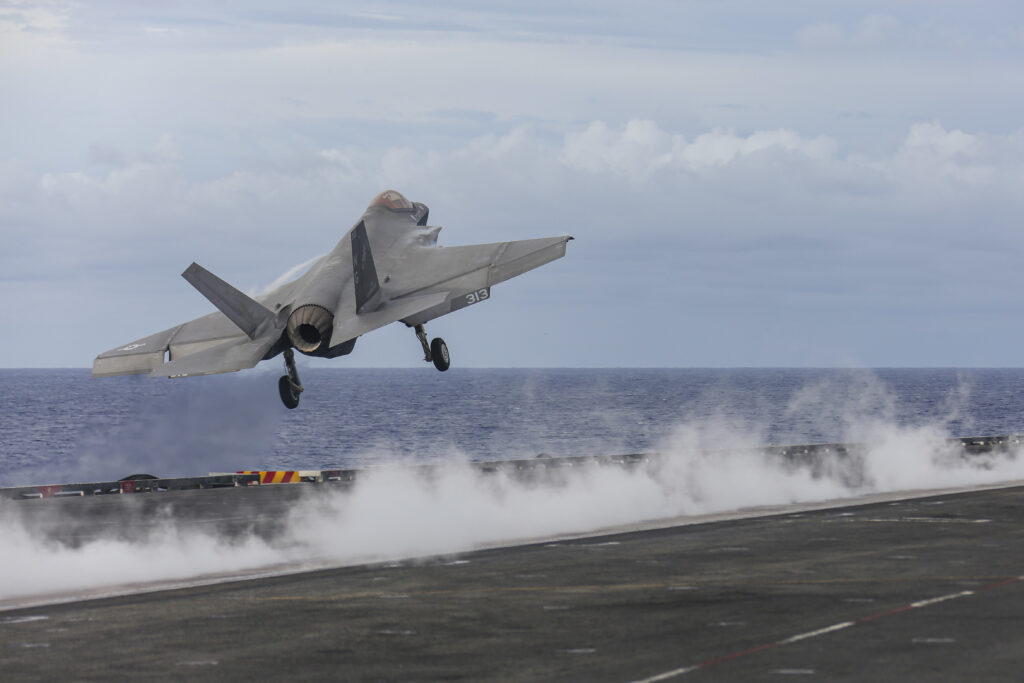
JACKSONVILLE, Fla. — Fleet Readiness Center Southeast (FRCSE) recently began activation as a Department of Defense second depot source of repair (DSOR) for the F135 engine, the propulsion system that powers the F-35 Lightning II Joint Strike Fighter. The first DSOR for the F135 was designated in 2012 with activation complete in 2014 at the Oklahoma City Air Logistics Complex, Tinker Air Force Base, Oklahoma.
“It’s great to be a part of the FRCSE Team as we prepare to activate the F135 engine product line,” said FRCSE’s Commanding Officer, Capt. Grady Duffey. “The new scope of work won’t just expand our support of the Joint Strike Fighter, but will help meet the sustainment demands of our military. I am confident that FRCSE will be ready to answer the call and commence repair of F135 engine modules in the near future, and at an even greater rate later as we expand infrastructure.”
FRCSE officially activating as second DSOR doesn’t come without certain challenges. Before the command sees its first Power Module (PM), one of the five major modules that make up the F135 power plant, artisans will need to go through a three-phase Pratt & Whitney (P&W) training and maintenance qualification and certification process, which is set to begin in January 2023.
The first two training phases focus on classroom and practical skills. The engine’s PMs and associated mini-modules (MMs) will be used to accomplish the hands-on portion of the training with artisans and P&W trainers working side-by-side.
Once the practical hands-on phase is complete, qualification and certification will be the final step in the process. FRCSE is expected to induct its first PM by April 1, 2023, with a second arriving about two weeks later.
After certification is achieved, F135 engine line artisans will work only on the PM and its four MMs — the high-pressure compressor, high-pressure turbine, low-pressure turbine and diffuser combustor — in designated areas called cells. The current plan is to have nine PM cells and 22 mini-module cells.
While FRCSE’s Crinkley Engine Facility complex currently performs work on four other engines (F404, F414, TF34 and J85), expansion is a must to support the full anticipated F135 workload.
“In preparation of this engine workload, we had to make multiple facility improvements along with purchasing new industrial plant equipment and machinery unique to the F135,” said Rick Eveson, FRCSE’s F135 production line director. “New high-capacity bridge cranes, a new entrance, floor paint and Andon lighting have all been procured to support the F135 engine maintenance process, which will also benefit our other engine programs. In addition, we’ve developed a custom shelving unit to more efficiently store parts, tooling and gear.”
FRCSE won’t just accommodate this new workload through the optimization of shops and processes in its current state, but also through the renovation of its existing engine test cell and construction of an entirely new engine facility by way of military construction (MILCON). A MILCON will be utilized in order to renovate FRCSE’s engine test cell as well as a whole new engine facility to streamline workflow. The new building is expected to break ground in 2026 with completion in 2028, and it will significantly increase the plant’s capacity for F135 work.
Furthermore, the engine test cell modification project will make significant changes to the existing structure, as the facility must be upgraded to accommodate the F135 engine’s 50,000 pounds of thrust and over 18-foot size. The building’s anticipated completion date is 2027.
“We expect engine production to ramp up through 2034 to the max production requirement — roughly 600 MMs and 120 PMs annually, correlating to about 600,000 man-hours,” Eveson continued.
From repair of the F135’s PM and its MMs to establishing depot capability for the F-35 airframe and associated systems, the command is certainly on its way to becoming the go-to facility in support of fifth and future generations of aircraft.
“The entire FRC Southeast team is excited to begin work on the F135 and showcase our world-class facility,” said Duffey. “We are unequivocally committed to this program’s success and to activating the U.S. Navy’s first F135 engine product line.”
- Red Sea Update - April 26, 2024
- U.S. Begins Construction on Temporary Pier to Deliver Humanitarian Aid to Gaza - April 26, 2024
- IKE Carrier Strike Group Arrives in the Eastern Mediterranean - April 26, 2024