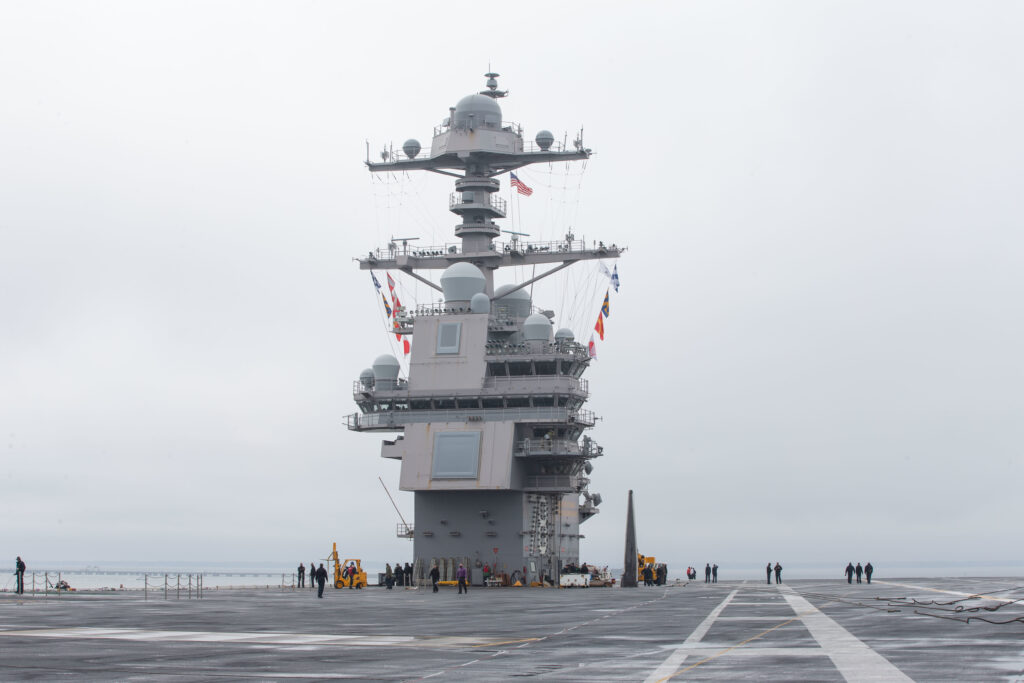
ARLINGTON, Va. — The Navy’s procurement and congressional funding of two Ford-class aircraft carriers in a single block buy enabled numerous small suppliers to weather or even survive the COVID pandemic, an industry official said. The stability of the program also enabled the aircraft carrier industrial base to control costs and enact savings.
Stable and predictable funding provided by the block procurement of CVN 80 and CVN 81, in place before the pandemic, gave the aircraft carrier industrial base the ability to absorb the shock of the pandemic, especially for the small lower-tier suppliers, said Rick Giannini, chairman of the Aircraft Carrier Industrial Base Coalition and CEO of Milwaukee Valve, speaking March 22 in a phone conference with Seapower.
“The two-carrier buy was really very helpful to the supply base [during the pandemic], because those orders in the hands of the suppliers before COVID gave them the work to get through things,” Giannini said.
Giannini said the ACIBC’s top priority is “stable and predictable funding,” which he defined as “a two-carrier block buy over eight years, with carriers purchased on four-year centers.
“And with that comes advance planning funding early in the cycle,” which he said “really is the catalyst. It’s great to have the bulk buy, but if we don’t have the funds to go and buy those raw materials as a supply base, it makes it very difficult to enact the savings that come out of it. We got good funding for [CVNs] 80 and 81, and one of the lessons is we need more early on so we can get more of the supply base involved.”
Giannini cited the experience of his own company, Milwaukee Valve.
“We were able to buy all of the materials for two full shipsets up front. Now we have that material in our facility so that the lead times not be impacted by material problems. Nor will the cost change. And it saves significant dollars and will improve the lead times overall.”
He said a two-carrier block buy is “very doable. We’re hoping we can get it moved up into 2024 — eight years after the AP [advance procurement] money came in for 80/81. We’re really trying to match the procurement of the Nimitz class. They were built on 3.5-year centers. So, four [-year centers] is good enough.”
The carrier industrial base coalition includes 2,000 companies from 46 states that employ approximately 121,000 workers. Its member companies provide $9.6 billion worth of materials and services for one aircraft carrier.
Workforce issues became prominent during the pandemic because many “baby boomer” workers retired earlier than planned. A shortage of skilled workers is focusing companies on recruiting and developing shipyard and manufacturing workers. Many companies are forming partnerships with local community and technical colleges and trade schools.
Giannini’s Milwaukee Valve company’s workforce is down about 8% in personnel, he said. Also, he noted that when a worker contracted COVID-19, about 10 other workers around that worker had to be quarantined, greatly affecting workflow for a week or two at a time. Absenteeism had risen to about 8 to 10 points on a fairly consistent basis, he said.
Giannini attended the dinner March 21 — sponsored by the Navy League —with Chief of Naval Operations Adm. Michael Gilday in Norfolk, Virginia, to celebrate the centennial of the U.S. Navy’s first aircraft carrier, where, he noted, the CNO said the Navy needed a force level of 12 aircraft carriers.