
Vice Adm. Bill Galinis, commander, Naval Sea Systems Command, responded to questions about the Naval Sustainment System – Shipyard from Senior Editor Richard R. Burgess.
What is the Naval Sustainment System – Shipyard?
GALINIS: Naval Sustainment System – Shipyard (NSS-SY) is a Navy corporate initiative focused on meeting our on-time ship and submarine delivery commitments at all our naval shipyards. This Navy-wide approach is designed to address all functional areas affecting execution performance in our public shipyards to include planning, material procurement, engineering, waterfront execution, facilities, information technology and fleet partnership. For years, we have struggled to deliver submarines and aircraft carriers back to the fleet on-time from scheduled maintenance periods. Over the last decade, we’ve worked to increase productivity by growing the size of our workforce, improving our training processes to accelerate learning and get our newest hires to the waterfront as quickly as possible. In working to improve the on-time performance of the shipyards we realized that we needed to rethink how we approached both the way we plan and execute the work.
At the heart of NSS-SY is the “get real, get better” approach. The direction provided in the CNO’s [Chief of Naval Operations’] Charge of Command to self-assess, self-correct and learn is clear. For us, that means that we need to look at our processes and procedures, understand where there are barriers that hinder or slow production work and then permanently remove them. To do this, we follow a stair-step process that empowers everyone from the deckplate or shop floor all the way up to me to fix issues or elevate them up the chain of command until it reaches the right level where the issue can be addressed. We call this the “fix or elevate” process, and it allows us to identify issues that prevent our production workforce from getting their job complete on time. The issue could be that our mechanics do not have the right tools, drawings or material on hand and we work with all of the Navy’s stakeholders — across the shipyard enterprise, NAVSEA, other Navy system commands, the fleet or Navy leadership as required — to ensure that our people have what they need, when they need it, so they can do their job.
Two additional important elements of the NSS-SY effort are the requirement to standardize practices across our naval shipyard enterprise. This includes starting with how we train our workforce, our business practices, material procurement efforts and work execution processes. There is tremendous opportunity in this area.
During this era of strategic competition, and when you consider the average cost of about $1 million per day to keep a submarine in a shipyard, every day matters when it comes to our availabilities. Every day of maintenance delay costs the Navy steaming days, training days, and forces other ships and crews to stay out longer. With NSS-SY, we are working to ensure that we maximize our skilled workforce so we can continue to deter aggression and win in a fight.
How and when did NSS-SY originate?
GALINIS: NSS-SY has its roots in Naval Sustainment System – Aviation when Naval Air Systems Command [NAVAIR] took on the challenge to have 80% of our F/A-18E/F Super Hornets and EA-18G Growlers mission capable. NAVAIR not only met but exceeded its requirement, and we in NAVSEA saw the goodness inherent in the NSS process and started applying it to our naval shipyards.
The level of complexity in maintaining a nuclear submarine or aircraft carrier is enormous, so we had to not just scale up what NSS-Aviation did, but really elevate the whole process to a new level. We worked diligently within NAVSEA headquarters and the naval shipyard enterprise to start the process. Initially leveraging the Navy’s Performance to Plan initiative focusing on data and data analytics to identify key deficiency areas, we learned pretty quickly that we needed to take a much more holistic approach that brought senior leaders from multiple NAVSEA equities, other Navy Systems Commands, the fleet and Navy leadership.
This process led to the establishment of the NAVSEA Transformation Office led by NAVSEA’s executive director Giao Phan and is comprised of nine pillars, each lead by a one- or two-star admiral:
• Engineering: Rear Adm. Jason Lloyd (NAVSEA 05)
• Planning: Rear Adm. Jim Downey (PEO CVN) and Rear Adm. Dave Goggins (PEO SSN)
• Materials: Rear Adm. Ken Epps (NAVSUP WSS)
• Inside Shops: Rear Adm. Scott Brown (NAVSEA 04)
• Waterfront Production: Rear Adm. Scott Brown (NAVSEA 04)
• Fleet Operations: Rear Adm. William Green (USFFC N43)
• Shipyard Resourcing: Rear Adm. Scott Brown (NAVSEA 04)
• Infrastructure: Rear Adm. Troy McClelland (PEO SIOP)
• Information Technology: Rear Adm. Huan Nguyen (NAVSEA 03).
Additionally, within each shipyard, aligned to the waterfront production pillar, we have established execution teams lead by “champions.” Our champions are senior, experienced shipyard personnel recognized as experts by leadership and their peers in the areas they are leading. This is really where the proverbial “rubber meets the road” and this team is driving the change we need inside our shipyards.
This team is working to ensure that we are aligned and working together, from NAVSEA headquarters to the shipyard waterfront to provide our skilled mechanics and trades with the material, training, equipment, technology and facilities required to execute their mission on time. These leaders are responsible for solving issues at their level and elevating issues as needed to improve the output of the naval shipyards.
Why the need for a change?
GALINIS: As CNO [Adm. Mike Gilday] wrote in his NAVPLAN, “There is no time to waste — our actions in this decade will set the maritime balance of power for the rest of the century.”
We are in an era of strategic competition with China and Russia. Both those countries are making significant investments in their navies and air forces to try and disrupt global dynamics and stability for their own economic benefit. Our Navy serves as the stabilizing force across the globe, and that is true because we are forward deployed and have the greatest Sailors and ships of any nation. Fleet readiness is top priority and foundational to executing our sea control and power projection missions. The work to provide our Navy and our country with materially ready submarines and aircraft carriers starts in our four public shipyards. Our naval shipyards are critical in ensuring that our submarines and aircraft carriers are materially ready to fight and win. NSS-SY is working to ensure that these front-line assets are delivered on time, every time so the fleet can meet its mission to preserve peace and win wars.
How is it an improvement on the way ship sustainment was done in the past?
GALINIS: The primary difference between NSS-SY and other efforts to improve naval shipyards’ performance is the whole-Navy approach we’re taking. No longer are we putting the onus on the individual shipyards to figure out how to improve. Instead, we are using metrics, data analytics, and workforce input to drive the procedural changes and business rule updates needed to ensure that we provide the production and engineering workforce with the full scope of what they need to be successful and make every day of a maintenance availability matter.
As I said earlier, we’re taking a holistic approach to how the naval shipyards are supported from across the entire Navy. Under Fleet Maintenance Officers Rear Adm. Greene and Capt. [Daniel] Ettlich, both former naval shipyard commanders, we are working with the fleets to improve our productive capacity within each shipyard by adjusting targets for our wage grade, or trade, personnel while also building a path to become a “master mechanic,” essentially providing a career in the trades with the appropriate level of training and compensation.
No availability can be completed on time if the planning and engineering isn’t done right, so Rear Admirals Downy and Goggins are working to improve our planning efforts by refocusing of planning milestone adherence and the quality and completeness of the planning products delivered to the shipyards. Rear Adm. Jason Lloyd has developed a team to address non-value-added requirements and “engineer work out” of availabilities to improve our on-time performance. Where the on-time procurement and delivery of material has proven to be one of our bigger challenges, and tied to our planning and engineering efforts, Rear Adm. Epps has implemented Material Planning Conferences tied to our availability planning efforts as well as rebuilding our rotatable pool processes.
On the infrastructure front, under Rear Adm. Nguyen, we’re working to improve our IT infrastructure to improve connectivity and information sharing while also working to upgrade computers at the four shipyards to improve productively and reduce unproductive time.
Adm. McClellan is executing the required physical infrastructure upgrades needed to execute maintenance in as efficient manner possible, with active projects in progress at Portsmouth and Norfolk and soon in Pearl Harbor and Puget Sound.
It all comes together on the waterfront and in our shops, and that is where Rear Adm. Brown is focused on a really, “back to basics” effort. As mentioned earlier, there are strong teams within each shipyard, led by our champions, working to implement the required change in this pillar. The focus here is to essentially rebuild our management and execution processes for executing complex ship maintenance and modernization efforts. Additionally, he has a strong effort in place to improve production shop performance, ensuring the production shop workforce has what they need to execute their mission.
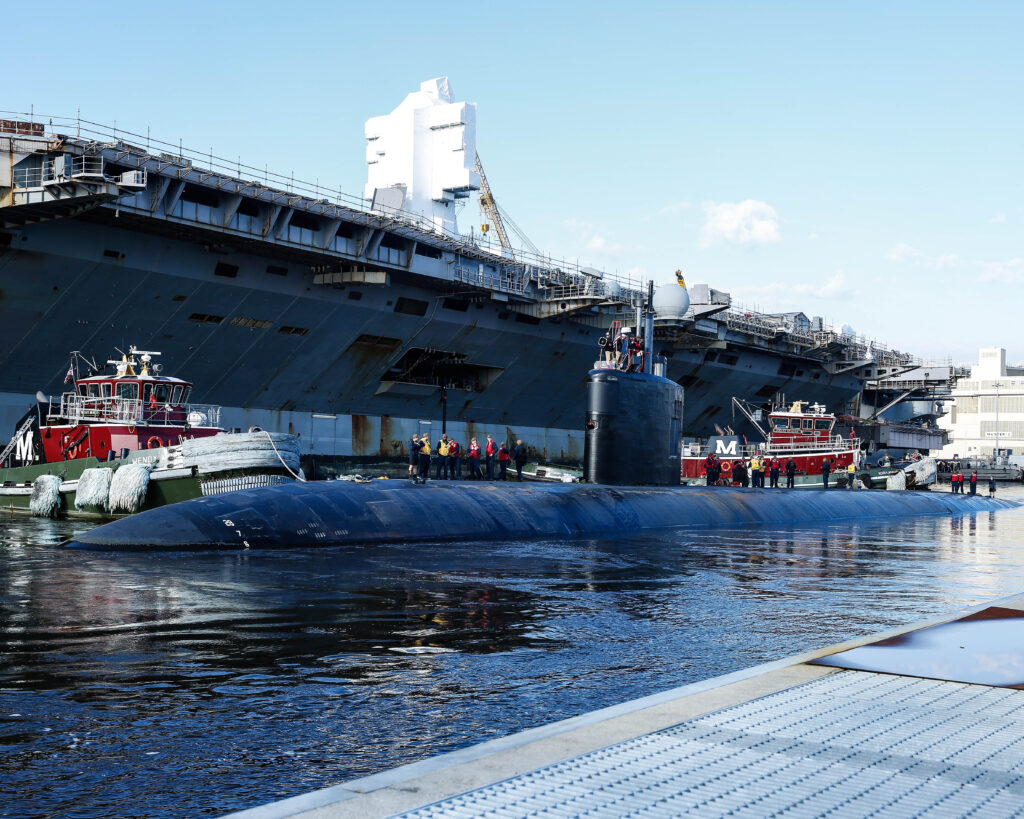
What are some of the lessons learned from the first four submarine pilot projects? Did they emerge from the shipyard on time?
GALINIS: Each shipyard has executed a number of initiatives we call sprints that are designed to quickly test ideas. During the first phase of NSS-SY, we focused on the waterfront production system and piloted OCC [Operations Control Center] and Start of Shift initiatives across four submarine CNO availabilities — USS Mississippi (SSN 782), USS Louisiana (SSBN 743), USS Virginia (SSN 774) and USS Pasadena (SSN 752).
Not every sprint resulted in positive outcomes. One example was our testing a new way to record work time for the production workforce. We thought we could remove some work hours at the supervisory level but, when we evaluated the pilot, we did not see the return on investment so we ended the pilot pretty quickly so we could put our efforts elsewhere. Although we don’t like to see our effort not pan out, it’s better that we fail fast so we spend more time in areas that may result in real time or energy savings.
A consistent theme in what we learned with the early efforts was a need to scale successful pilots quickly — the crew boards for example. Our approach here will be to implement pilot efforts where we see the need for improvement, quickly assess the impact of these pilots, and, if they work, scale them quickly across the four naval shipyards.
Our near-term efforts are really focused on the waterfront pillar to rebuild and reinforce the importance of our project management fundamentals. Improving our waterfront execution efforts, combined with near-term wins in material, engineering and IT, is where I believe we will have the most impact on avails in progress.
Looking a little further out, improving our planning efforts, getting this planning done on time with the requisite level of quality, combined with improved on time material procurement and delivery will be impactful. This will also improve our ability to manage the production work during a submarine or aircraft carrier availability.
Have you started any follow-on (post-pilot) availabilities using NSS-SY? Have you expanded beyond applying it to submarines?
GALINIS: Yes, we have. For example, we’ve established operational control centers that have been fully implemented for all CNO availabilities in progress and even into some of our shops.
The operational control centers are integral to our fix or elevate approach as issues identified at the waterfront or shop floor are sent there for evaluation and are either fixed or moved up the chain of command. It allows the project teams and trades a single place to send issues they cannot address themselves and serves as a way to bring subject matter experts together into a single space to investigate and address productivity barriers. This effort has driven down work stoppages in terms of numbers and durations on the waterfront and shown some improvement in getting decisions to the waterfront faster.
We’ve also continued to mature the use of crew boards across our availabilities, incorporating feedback from the waterfront. These crew boards lay out what specific work teams should accomplish that day. In establishing this daily goal, our tradespeople can better understand what they need to do and make every day matter. It also helps to track the status of ongoing work and help identify barriers to completion.
Additionally, the work being done within the waterfront pillar to improve and strengthen work execution principles, what we refer to as “project management fundamentals,” or PMF, has been very important. PMF is the tactical process used by our project teams to manage work execution during ship maintenance availability. The team is taking a back-to-basics approach to strengthen the training and understanding of these fundamentals, reinstill consistency of implementation and adherence, measuring throughput and incorporating commercial best practices where appropriate. This is one of our top focus areas to improve availability execution in the near term.
What metrics do you use to assess the success of availabilities under NSS-SY?
GALINIS: Ultimately, the only metric that counts is the number of days of maintenance delays. Our goal is to deliver all availabilities on time by 2023.
We have identified a number of metrics that we know will lead to a decrease in the number of days of maintenance delays. For example, we are looking at on-time task completion, how much production work is accomplished each day as compared to a daily schedule, and how much we are reducing unplanned work, or work that is not identified prior to the start of the availability. We are constantly reassessing how we measure ourselves to ensure we stay focused on the right measurements and tasks.
We also have tangential information about our workforce’s buy-in to the program. When we first started rolling out crew boards, they did not go to every shop on every availability. Instead, we tested the concept with a couple shops on a couple availabilities. One day, a supervisor walked past a crew board, saw the goodness and value in sharing that information, and on his own built his crew their own crew board. When you have that type of buy in to a concept, you know you’re on to something good.
What new technology, if any, has been introduced as part of NSS-SY?
GALINIS: While NSS-SY is principally focused on improving our business and production practices, and I discussed the importance of standardizing of our practices, equally important is our ability to innovate and improve our processes as well as bring in new technology. We have consistently encouraged and challenged our shipyard to look for improvement opportunities.
A good example of driving innovation into our work practices is the current friendly competition between Portsmouth and Pearl Harbor Naval Shipyards on Virginia-class work practices to drive time and cost out of these availabilities.
On the technology front, we stood up an Engineering Intervention Board to more efficiently and quickly evaluate new technologies as part of its effort to remove schedule and cost from availabilities. And many of these new ideas come from the waterfront.
Examples of technologies the EIB is currently evaluating include an automated condenser cleaning system that cleans condenser tubes while saving substantial time. We are also looking into an autonomous grit-blasting system that also reduces the workforce requirements. Same for a phased array ultrasonic non-destructive testing technique and laser ablation that removes rust and other materials with a laser beam and not a wire brush or wire wheel.
What are the cost advantages, if any, demonstrated by the NSS-SY projects?
GALINIS: NSS-SY is focused on improving business practices within the shipyards and maximizing the productive time of our artisan and engineering workforce. It’s about on-time work completion that results in on-time deliveries and therefore on-cost deliveries as well. From a shipyard perspective, providing our waterfront mechanics/trades the right material at the right time, the right tools, technical information, etc., will allow them to be more efficient. The more effective we make our skilled tradespeople, the quicker they can complete a job and then move to the next one, which reduces the number of work hours and days in an availability, and the quicker we can buy back idle time for the ships and their crews.
That said, there is a cost component to delivering ships on time. For every day a submarine is delayed in an availability, the Navy expends about $1 million. That includes all the operational costs for the boat. For aircraft carriers, that figure doubles to $2 million. When the ship and its crew is in the shipyard, the Navy is not getting productive capacity from its investment.
Similarly, there is a readiness deficit that we run when we do not deliver on time. For the delayed ship and its crew, that’s less time working together as a team, at sea, where they need to be to gain true warfighting proficiency. It also causes us to run deployed crews and their ships longer and harder than we want and that has an impact on our people and warships.
Ultimately, NSS-SY is about delivering ships on time, every time but ensuring our workforce has what they need, when they need it, to get the job done.
What feedback are you getting from the shipyard workers on NSS-SY?
GALINIS: The feedback has been positive. As with every new concept it takes a while for people to really understand what we’re doing and why we’re doing it. We are really starting to see the momentum build for the NSS-SY efforts. We need to drive the credibility and ownership of this effort to the waterfront. The credibility piece will be built by demonstrating how these initiatives make the job easier for our tradespeople by ensuring they have the right material when they need, they have the right work sequence, correct technical drawings and the ownership element. We are seeing now where the shipyards are using the NSS-SY efforts to drive improvements in the shipyards.
Frankly, our shipyard personnel were a little guarded about NSS-SY to start. They have seen other attempts to improve productivity that have had limited success. Additionally, there was some who thought NSS-SY was going to add an already high workload. While there is some investment/work upfront required, the bottom line here is that the improvements we are making need to make it easier for our naval shipyard waterfront teams to meet their commitments. NSS-SY is about making these teams successful. The focus here is to remove barriers and provide the resources required to enable them to do their job safely and on-time.
Our naval shipyards are national assets, and our people are the heart and soul of this enterprise. We have a leadership team aligned on the imperative to improve — to get real and get better. The shipyard team is committed to meeting our commitments to the fleet in terms of on time delivery. Through the NSS-SY effort, we have developed a process to improve our execution performance, measure our improvements and correct where required and hold ourselves accountable for sustaining this performance across our naval shipyards.
How does NSS-SY relate to the Shipyard Infrastructure Optimization Program?
GALINIS: NSS-SY and SIOP share the same goal of setting our public shipyards up for long-term success with success being measured in the on-time delivery of submarines and aircraft carriers out of maintenance availabilities.
SIOP is focused on recapitalizing the physical infrastructure — upgrading the dry docks and the shipyard infrastructure to include our shop facilities, and then the industrial plant equipment, all required to execute maintenance on new classes of submarines and aircraft carriers.
NSS-SY, on the other hand, is about updating our business practices, work execution processes and procedures to support the on-time execution of ship availabilities and ensure our mechanics and engineers have the tools and material they need to safely execute their work on time and with minimal or no delays.
Separately, NSS-SY and SIOP will result in substantial positive changes within the naval shipyards. When you combine NSS-SY and SIOP together, you have the truly fundamental and unprecedented investment that our shipyards require to execute maintenance on time, every time for generations to come.
Do you foresee expansion of NSS-SY concepts to private shipyards for Navy ship availabilities?
GALINIS: Yes, I do, and in fact we are sharing best practices and lessons learned from our NSS-SY efforts with our counterparts in the private sector. A component of NSS-SY is the Navy adopting industry best practices in order to become more efficient. That said, it will only benefit the Navy to share our best practices with our ship maintainers and builders.